Master Reactive Extrusion in Twin Screw for Enhanced Quality & Safety
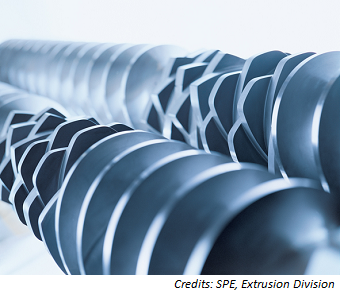
Package Includes
6 months access to Course Recording, Presentation Slides, Q&A Transcript
Course Description
Get started with reactive extrusion for your thermoplastics by gaining a 360⁰ view of the process, the reaction chemistry, and how to configure the extruder.
In this simulated live course, Kenneth Russell will help you spend less time on trial and error and develop materials with reactive extrusion principles and practices faster by sharing hands-on tips on injecting liquids, defining the right residence time distribution (RTD), and more.
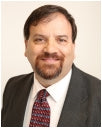
Kenneth W Russell
Why should you view this course?
Who should join this course?
-
This course is suitable for beginner level proficiency
Beginner
Course Outline
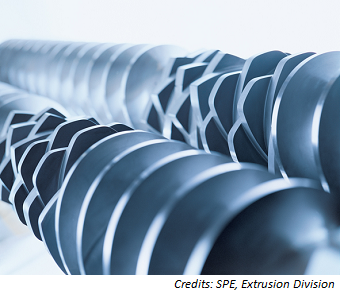