Product Improvement
Rigid PVC: How to Maximize Performance to Cost Ratio
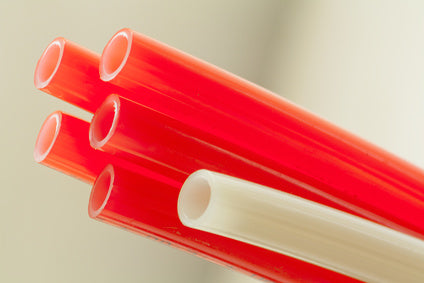
Language: English
Length: 75 min
Recorded on: 23 Oct 24
Package Includes
6 months access to Course Recording, Presentation Slides, Q&A Transcript
Course Description
Achieve demanding end use / regulation requirements with your rigid PVC while minimizing costs. Overcome challenges of changing additives or processing scale in demands like larger pipes, high temp., and REACH regulation on tin stabilizers…
To help you reach desired performance (high temp. resistance, impact strength…) leading expert Paul Mastro in this simulated live (>30 years of experience) will guide you on:
To help you reach desired performance (high temp. resistance, impact strength…) leading expert Paul Mastro in this simulated live (>30 years of experience) will guide you on:
- How additives (stabilizers, lubricants…) work & their impact
- Latest regulations (NSF for potable water pipes, UL 94 for electrical conduits, fittings...)
- Correlation between process & formulation of rigid PVC
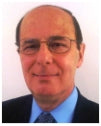
Paul Mastro
0 courses
See Tutor Profile
Why should you view this course?
Who should join this course?
-
This course is suitable for intermediate level proficiency
Intermediate
Course Outline
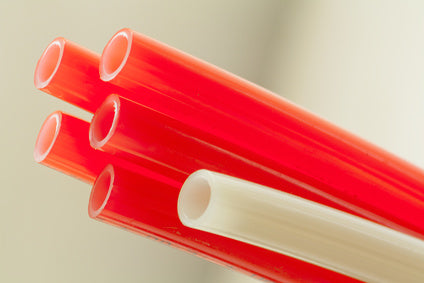
Share this Course
Share this Course
https://courses.specialchem.com/products/rigid-pvc-how-to-maximize-performance-to-cost-ratio